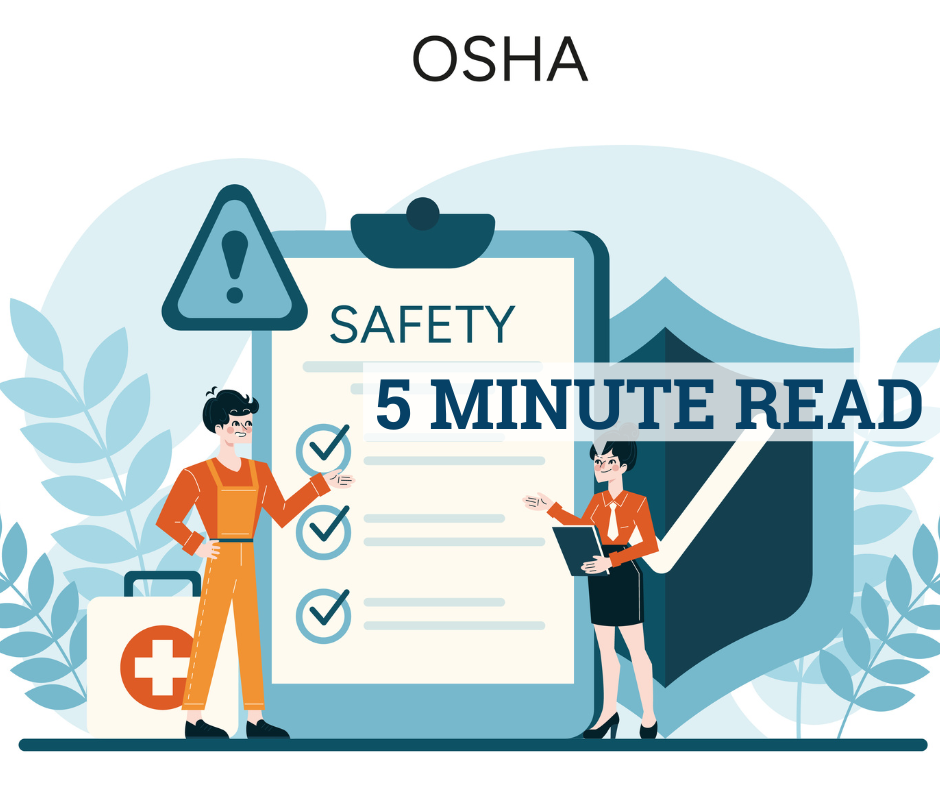
Don’t wait until it’s too late. Take action now to ensure your workplace is prepared for OSHA inspections before they arrive.
Workplace safety isn’t something that should be addressed only when an inspection is at your door. Being proactive is key to preventing violations and ensuring the well-being of your employees. In the first part of this series, we explored what triggers Occupational Safety and Health Administration (OSHA) inspections. Now, we’ll shift our focus to practical steps you can take to prepare well ahead of time, so that when an inspection occurs, you’re ready to face it with confidence rather than concern.
Why Preparation Matters
Just as you’d service machinery before it breaks down, it’s vital to address safety and compliance before OSHA comes knocking. Proactive preparation can help:
- Prevent financial setbacks: Early improvements may cost less than hefty fines and emergency fixes.
- Ensure employee well-being: A safer environment reduces the likelihood of serious injuries or fatalities.
- Enhance workplace culture: A proactive approach builds trust and shows employees that their safety matters.
Build A Safety-First Culture
A positive safety culture is the foundation of any successful preparation plan. When everyone from top management to entry-level employees understands their role in maintaining a safe environment, compliance becomes second nature. Encourage open dialogue about safety issues, hold regular ‘toolbox talks’, and celebrate examples of conscientious behavior. The goal? To make safety part of your company’s identity, not just a line item on a checklist.
Conduct Thorough Safety Audits
If you’ve never conducted a comprehensive safety audit, now is the time. Systematically review your facilities, equipment, and workflows to identify any hazards or compliance gaps. Pay special attention to areas that frequently trigger inspection, like fall protection, machine guarding, and hazardous material handling. Consider bringing in third-party experts if necessary. These professionals can spot overlooked risks, offer practical solutions, and help ensure you meet OSHA standards.
Develop Clear Policies And Procedures
If your employees don’t know what’s expected of them, they’re more likely to take shortcuts or unknowingly violate safety standards. To avoid this, make sure to:
- Draft and update safety policies: Keep documentation in plain language so everyone understands it.
- Post guidelines prominently: Place safety reminders and protocols in high-visibility areas, such as break rooms and job sites.
- Establish reporting channels: Make it easy for employees to report hazards or concerns without fear of backlash.
By putting strong policies in place, you create a roadmap that guides everyone toward safer work habits and ensures that no one’s left guessing what the rules are.
Prioritize Training And Communication
Even the best policies won’t help if employees aren’t aware of them or don’t know how to apply them in real-world scenarios. To ensure that employees are aware of your company’s safety protocols, consider utilizing:
- Onboarding sessions: Introduce new hires to your safety culture and outline their responsibilities from the start.
- Hands-on workshops: Practical training helps employees recognize hazards and use protective equipment correctly.
- Refreshers and updates: Industries evolve, and so do regulations. Stay compliant by hosting regular retraining sessions to align with evolving regulations.
Regular communication keeps safety top-of-mind. Consider monthly newsletters, safety bulletins, or short videos highlighting new techniques or reminders. The more accessible and engaging your training materials, the better your employees will retain and apply them.
Keep Meticulous Records
From injury logs to training certifications, can make or break your compliance efforts. If an inspector arrives, well-organized records show that you’ve been diligent. These records include:
- Accident and incident reports: Promptly record any workplace injuries, near-misses, or other safety-related events.
- Training verification: Maintain a record of all completed training sessions, who attended, and when.
- Equipment maintenance logs: Show that machinery and safety equipment are regularly inspected and maintained.
- Hazard assessments: Keep a written record of identified risks and the steps taken to address them.
Good recordkeeping not only helps you during an inspection; it also supports continuous improvement. By reviewing past incidents and training outcomes, you can identify trends, refine your policies, and make targeted changes that reinforce workplace safety over time.
Conduct Mock Inspections
Don’t wait until an OSHA representative is actually on-site to find out where you’re falling short. Conducting mock inspections, either internally or with outside consultants, helps you see your operation through the eyes of an inspector. Walk through your facility, check for compliance with known OSHA standards, and evaluate how well employees follow safety protocols. Mock inspections can:
- Highlight weaknesses: Identify issues before they escalate into violations.
- Improve response time: Familiarize your team with what to expect, so they remain calm and cooperative during a real inspection.
- Build confidence: By knowing you’ve addressed potential pitfalls, you can approach a real inspection with assurance.
Partnering With GMS For A Proactive Approach
Staying ahead of OSHA compliance can feel overwhelming when you’re already managing day-to-day operations. That’s where Group Management Services (GMS) can step in. Our experts can help your business:
- Conduct audits and gap analyses: We’ll identify areas where you may be at risk before an inspector does.
- Refine training programs: Gain access to resources that keep your team informed and prepared.
- Support recordkeeping and documentation: We’ll help ensure your paperwork is in order and easy to reference.
By partnering with GMS, you’re not just preparing for an inspection, you’re cultivating a robust, ongoing approach to safety. This proactive stance empowers your workforce, strengthens your compliance efforts, and sets you and your business up for long-term success.
Contact GMS today to learn more about how we can support you in preparing for and preventing OSHA inspections. Click here to continue reading how to handle OSHA when they finally come to inspect your workplace.