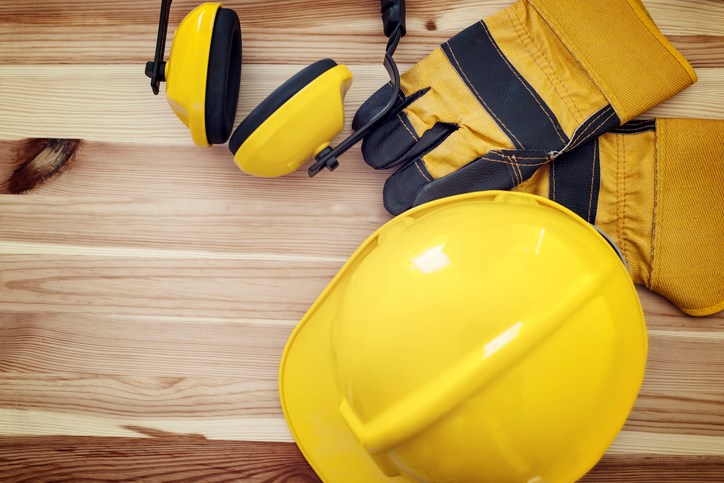
Workplace safety is essential for any business, but it takes on even more importance for construction workers. According to OSHA, nearly 20% of private industry worker fatalities were in the construction industry. That inherent danger is exactly why safety meetings are a critical tool for any construction company.
Regular construction safety meetings, often referred to as toolbox talks, are a key part of any safety program. Sharing the right construction site safety tips during these meetings can help protect people, keep your company compliant, and reduce workers’ compensation costs. That’s why it’s essential to educate employees and keep everyone on the same page about a variety of topics.
What To Discuss During Your Construction Safety Meetings
Every meeting is an opportunity to tackle important safety concepts, topics, and guidelines that will keep your employees healthy and productive. Whether you plan to tackle a variety of subjects in one meeting or want to dedicate an entire session to a specific theme, consider these nine construction safety meeting topics to share at your next meeting:
- Personal protective equipment (PPE)
- Fall protection
- Hazard identification
- Lockout/tagout
- Hand and power tools
- Fire safety
- First aid
Personal protective equipment (PPE)
Good preparation is pivotal. Personal protective equipment (PPE) is designed to minimize an individual’s exposure to various hazards that can cause serious injuries and illnesses while they’re in the workplace. PPE comes in many forms that range from hard hats to full body suits, but every piece of PPE plays a role in protecting your team.
Employers are required to provide workers with any necessary PPE to complete their job, along with proper training and guidelines on how to use each piece of PPE. A construction safety meeting is an excellent place to educate employees on your PPE program. That process includes discussing the following PPE-related topics.
- When PPE is necessary.
- The types of PPE that are necessary in different situations.
- How to properly put on, adjust, wear, and take off PPE.
- The limitations of PPE.
- Proper care, maintenance, useful life, and disposal directions for PPE.
Fall protection
Slips, trips, and falls are a hazard in any setting, but the construction industry is especially at risk. According to the Centers for Disease Control and Prevention (CDC), construction accounts for roughly half of all on-the-job falls and more than one-third of fall-related fatalities. Discussing the following construction site safety topics with your employees can help your business reduce or eliminate these types of accidents.
- An overview of fall protection.
- Common fall hazards and hazard recognition.
- The different forms of passive and active fall protection.
- On-site fall safety requirements for different worksite environments.
- Training on how to proceed around fall hazards and how to use appropriate equipment.
- What to do if there is a fall.
Hazard identification
OSHA defines a hazard as “an inherent property of a substance that is capable of causing an adverse effect.” Simply put, hazards qualify as anything that can hurt someone in your workplace and need to be identified as quickly as possible. Safety is a team effort, which is why hazard identification should be a notable topic for an upcoming safety meeting.
Teaching employees about hazard recognition is a process that goes beyond spotting danger. Take the following steps the next time you highlight hazard identification during a toolbox talk.
- Educate employees on the definition of the term “hazard” and how it applies to them.
- Highlight the different forms hazards can take in the workplace and provide relevant examples. These include:
- Physical hazards – Excessive noise, cutting risks, etc.
- Chemical hazards – Exposure to toxic substances, accidental ingestion, etc.
- Airborne hazards – Fumes, gas leaks, etc.
- Ergonomic hazards – Improper lifting techniques, improper posture, etc.
- Biological hazards – Mold, bacterial growth, etc.
- Practice hazard identification with employees through demonstrations and other tests like OSHA’s Hazard Identification Training Tool.
- Share the appropriate process for when an employee spots a hazard, including:
- How to communicate with the team about a hazard.
- Assessing the risk of the hazard.
- Putting controls in places to eliminate or reduce the hazard’s ability to cause harm.
Lockout and tagout
Heavy equipment and machinery are not uncommon in the construction industry, but they can pose a threat if not dealt with appropriately. Proper lockout and tagout procedures can help employees safely depower these machines to prevent future injuries.
A safety topics for construction meeting is an excellent opportunity to educate employees about proper maintenance and service protocol. Present written lockout/tagout procedures for every machine during the meeting (and create them if they don’t exist). You’ll also want to walk through the exact procedures for any relevant machines. For example, the following steps represent a typical lockout/tagout process:
- Notify employees affected by lockout/tagout procedures.
- Shut down equipment according to written guidelines.
- Isolate the energy source.
- Attach the appropriate lockout device.
- Release or restrain any energy stored in the machine.
- Verify the lockout with the proper personnel.
Hand and power tools
Heavy equipment isn’t the only potential danger on a job site. Common construction tools and other machines can pose hazards without proper training and use. Employers can use safety meetings as a refresher courses for existing tools, special sessions for new devices, or a combination of both. Regardless, the following topics are good subjects during these meetings:
- How to keep all tools in good condition through proper storage and regular maintenance.
- How to select the right tool(s) for each task or job.
- How to examine tools for any damage or other warning signs prior to use.
- Correct operating procedures for each tool (including manufacturers’ instructions if applicable).
- How to spot environmental issues that can impact tool safety (ex. wet conditions for electrical equipment).
- When and how to properly use the right PPE for relevant tools.
Fire safety
Between electrical tools and flammable materials, fires are a real risk on many construction sites. A fire can break out at any time, so it’s best to educate employees about what they can do to prevent them – and what to do in case one does occur. Below are some notable topics that your business should discuss during a fire safety toolbox talk.
- Common job site fire safety hazards.
- How to handle and store flammable materials.
- How to use equipment that can create sparks and other potential fire safety issues.
- Proper procedures during a fire and other related response plans.
- Where to find fire response equipment (and how to use that equipment).
First aid
While businesses can take several precautions to make their work environment as safe as possible, there’s always a chance someone can get hurt. OSHA requires construction companies to have someone properly trained in first aid on-site, but it’s also good to remind workers about first aid basis. That discussion should include the following topics:
- The location of any first aid kids on-site and what these kits contain.
- Any other safety supplies that may be required on-site, such as an automatic external defibrillator.
- How to use first aid skills for minor treatments, such as cleaning minor cuts, applying bandages, and more.
- A review of your emergency action plan, including the following steps:
- How to survey an accident scene.
- How to identify injuries and other issues.
- How to contact emergency medical services (and what information you should share with them).
Take A Proactive Approach To Workplace Safety Management
From ladder safety to hazard recognition, a little prevention goes a long way toward protecting your employees and business from injuries, illnesses, and worse. Construction safety meetings are an excellent way to train workers, encourage discussion, and keep everyone accountable. Unfortunately, it’s not always easy to stay ahead of safety and compliance risks alone.
Group Management Services partners with businesses to make their business safer and more efficient. Our workplace safety experts take a proactive approach through onsite consulting, jobsite inspections, workplace safety courses, and other key services. Contact us now about how GMS can make your business a safer place.